Hybrid Generator Would Cut Military Base Fuel Costs in Half
By Martin LaMonica
Posted 3 Feb 2014 | 20:38 GMT
By Martin LaMonica
Posted 3 Feb 2014 | 20:38 GMT
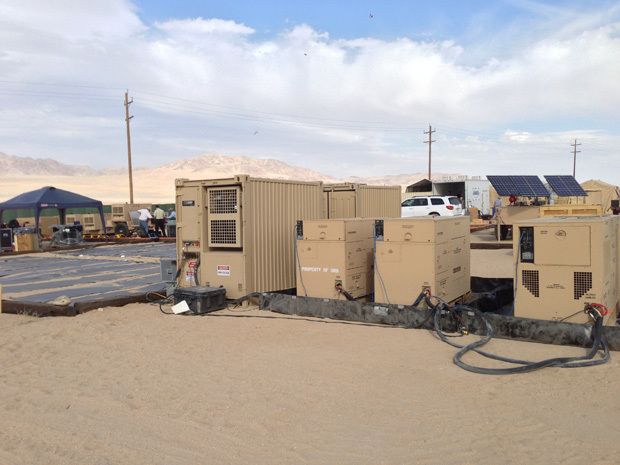
http://spectrum.ieee.org/energywise...or-would-cut-military-base-fuel-costs-in-halfThe phrase "An army marches on its stomach," often attributed to Napoleon Bonaparte, underscores the importance of logistics in the military. And in the 21st century, keeping up the supply of diesel fuel is one of the most challenging logistical tasks for military forces in the field.
Last month, the U.S. Department of Defense (DoD) awarded a contract to a company that says its “hybrid generator” can reduce the amount of fuel used by generators at outposts by more than 50 percent. The company, Earl Energy, uses a rack of batteries coupled to diesel generators—and, if available, solar panels—to optimize fuel consumption. It’s one of a number of projects funded by the Department of Defense to reduce fuel consumption through efficiency and renewable energy.
Today, the U.S. military powers its operating bases with diesel generators that run continuously. The problem is that it’s difficult to match the generating capacity with the actual power load from air conditioners, electronics, and other gear, which fluctuates during the day and in different seasons. And when the demand for power is lower than the generator’s full capacity, the fuel efficiency drops off dramatically and the maintenance increases.
At the same time, the electricity requirements for bases in places such as Afghanistan have gone up substantially. Compared to a Marine battalion a decade ago, bases now have more than twice the number of radios and vehicles and three times the number of computers, according to the Department of Defense.
Earl Energy’s FlexGen “hybrid generator” is wired to a diesel generator running at full capacity, which is how it's most efficient. When there is excess power, the diesel generator charges the batteries. If the batteries have enough stored energy to meet the demand for electricity, then the generator shuts off. In tests in Afghanistan, the Earl Energy system allowed the generators to run three to six hours a day, compared with around the clock before it was installed, says Doug Moorehead, the CEO of Earl Energy.
A former Navy Seal, Moorehead saw first hand the perils of transporting fuel while stationed in Iraq. Fuel and water convoys are frequent targets. For example, in one three-month period in 2010, six marines were wounded during convoys (a rate of one injury for every 50 convoys). The financial cost is great as well; fuel can cost $2.64 to $3.96 per liter ($10-$15 per gallon) by the time fuel is delivered to outposts, says Moorehead. "If you reduce the fuel consumption, you can now cut [the number of fuel convoys] in half,” he says.
After Moorehead’s time in the Navy, the MIT graduate attended Harvard Business School and then went to work at lithium-ion battery company A123 Systems, where he worked in the grid energy storage group.
With funding from a previous Department of Defense program, Earl Energy was able to build prototypes for its energy storage device. It now has about a dozen units in the field, which are partially charged with energy generated by solar panels. The system’s control software can be used to manage multiple generators in order to create a base-wide microgrid.