http://www.spacedaily.com/reports/A...clothes_for_potential_broad_adoption_999.htmlA new lightweight, low-profile and inexpensive ankle exoskeleton could be widely used among elderly people, those with impaired lower-leg muscle strength and workers whose jobs require substantial walking or running.
Developed by Vanderbilt mechanical engineers, the device is believed to be the first ankle exoskeleton that could be worn under clothes without restricting motion. It does not require additional components such as batteries or actuators carried on the back or waist.
The study, published online by IEEE Transactions on Neural Systems and Rehabilitation Engineering, builds on a successful and widely cited ankle exoskeleton concept from other researchers in 2015.
"We've shown how an unpowered ankle exoskeleton could be redesigned to fit under clothing and inside/under shoes so it more seamlessly integrates into daily life," said Matt Yandell, a mechanical engineering Ph.D. student and lead author of the study.
In a significant design advancement, the team invented an unpowered friction clutch mechanism that fits under the foot or shoe and is no thicker than a typical shoe insole. The complete device, which includes a soft shank sleeve and assistive spring, weighs just over one pound.
The unpowered ankle exoskeleton costs less than $100 to fabricate, without factoring in optimized design for manufacturing and economies of scale.
"Our design is lightweight, low profile, quiet, uses no motor or batteries, it is low cost to manufacture, and naturally adapts to different walking speeds to assist the ankle muscles," said Karl Zelik, assistant professor of mechanical engineering and senior author on the study.
Zelik will be presenting this work next week at the Wearable Robotics Association Conference in Phoenix, Arizona.
The potential applications are broad, from helping aging people stay active to assisting recreational walkers, hikers or runners, he said.
"It could also help reduce fatigue in occupations that involve lots of walking, such as postal and warehouse workers, and soldiers in the field," Zelik said.
Joshua Tacca, BE'18, also is a co-author. He is now a graduate student in the Integrative Physiology Department at the University of Colorado-Boulder. Several other Vanderbilt undergraduate engineering students also contributed to the device design and pilot testing.
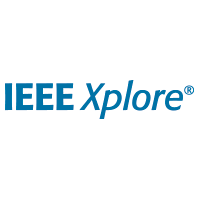
Design of a Low Profile, Unpowered Ankle Exoskeleton That Fits Under Clothes: Overcoming Practical Barriers to Widespread Societal Adoption
Here, we present the design of a novel unpowered ankle exoskeleton that is low profile, lightweight, quiet, and low cost to manufacture, intrinsically adapts to different walking speeds, and does not restrict non-sagittal joint motion; while still providing assistive ankle torque that can reduce...