LÄHDE
3UBM5
3BM6
Introduced in service in either 1964 or 1966, or some time in between, the 3UBM5 cartridge with the 3BM6 projectile was a slightly more advanced but similarly cheap alternative to the 3UBM4 round that could approach the flat penetration power of 3BM3 while offering equivalent penetration power on sloped armour. Like 3BM4, the 3BM6 projectile featured an armour-piercing cap. It officially replaced both the 3UBM3 and 3UBM4 rounds by the mid-1960's - a technical manual for the T-62, approved for distribution on the 14th of January 1967, only mentions 3UBM5 and an unknown 3UBM6.
Between 1966-1968, a new model of 3BM6 projectile without an armour-piercing cap began replacing the older type. Knowing this, the 3UBM5 round must have entered service before 1966.
Externally identical, the 3BM6 projectile can be distinguished from the 3BM4 by the presence of knurls on the rim of the "ring" type sabot which are absent from the one on the 3BM4 projectile. The presence of these knurls can be connected to the creation of the T-64 medium tank with a 115mm D-68 gun, which uses an autoloader. These knurls were needed to ensure the smooth loading of the projectile into the D-68 gun chamber by a mechanical powered rammer, which can only push the cartridge along the surface of the chamber where the possibility of the projectile getting stuck against the shoulder of the chamber neck may arise.
For the manually loaded U-5TS gun, a human loader can insert a cartridge while taking care not to scrape the shoulder of the projectile against the chamber walls, which is why the sabot for 3BM3 and 3BM4 did not have knurls.
Before the introduction of 3UBM5, a series of new two-part 115mm rounds was created in 1964 for the T-64, which had the new D-68 gun. Alongside the T-64 itself, a new set of ammunition entered service in 1966. Among them was the 3BM5 projectile, which was part of at least two cartridges in at least one form. It was a part of 3VBM1 from 1964, and 3VBM5 from 1970, where it had no armour-piercing cap. The 3BM5 was not used in the single-part ammunition for the U-5TS, but 3BM6 had an almost identical design. The knurled sabot used on 3BM6, with six interface grooves, was very similar and possibly the same as the sabot for
the early 3BM5 projectile for 3VBM1.
Internally, they are quite different.
The penetrator is made from 35Kh3NM steel with a hardness of around 600 BHN. The 35Kh3NM grade of steel had been in use in standard full-caliber armour-piercing shells like the 100mm BR-412B and 122mm BR-471B since their creation in the late stages of WWII. Naturally, the hardening of the steel to around 600 BHN is consistent with the hardening of the older full-caliber shells of postwar production. The 3BM6 penetrator had a rounded nose and it had an armour piercing cap made from softer 35KhGS steel with a hardness of 451-552 BHN. Although still made entirely of steel, this shell offered appreciably higher performance on oblique steel plate but was still not on par with the 3BM3 on flat targets. The stabilizing fins are made from 40KhFA steel alloy with high thermal resilience. The fin assembly weighs a total of 0.651 kg.
Here is what the penetrator without the armour piercing cap and the windscreen (ballistic cap) looks like:
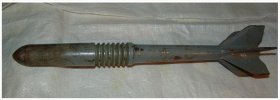
The propellant charge consists of 8.1 kg of 12/7 granular and 18/1 tr. tubular propellant exclusively - DG-4 was not used with 3UBM5. Due to the lower calorific value of the new propellant mix, counterbalanced by its increased efficiency, the internal ballistics with the new propellant did not change. As such, although 3BM6 had a slightly increased muzzle velocity of 1,680 m/s, higher than both 3BM3 and 3BM4, this was merely due to its slightly lower projectile weight.
Projectile Maximum Diameter: 42mm
Diameter of Stabilization Fins: 114mm
Total Projectile Length: 550mm
Total Cartridge Length: 950mm
Penetrator Length: 436mm
Mass of Complete Round: 21.66 kg
Total Projectile Mass: 5.34 kg
Mass of Subcaliber Projectile: 3.86 kg
Mass of Steel Penetrator: 3.009 kg
Mass of Armour Piercing Cap: 0.167 kg
Muzzle Velocity: 1,680 m/s
Penetration at 1,000 meters:
280mm RHA at 0°
135mm RHA at 60°
Penetration at 2,000 meters:
240mm RHA at 0°
110mm RHA at 60°
The new armour piercing cap appears to have improved the performance of the projectile on sloped armour to the point where it is superior to the BM3, making this shell even more useful than its predecessor on the heavily sloped armour of contemporary NATO tanks like the Chieftain and the M60A1. The graphs below, taken from the book "
Частные Вопросы Конечной Баллистики" from 2006 (
Particular Questions of Terminal Ballistics) published by Bauman Moscow State Technical University on behalf of NII Stali, shows the penetration curve of three different subcaliber ammunition types, each representative of different classes. 3BM6 is represented as the dotted and dashed line. The impact velocity for all three ammunition types is 1,500 m/s, which corresponds to a distance of between 1,200 and 1,600 meters. The y-axis shows the thickness of armour defeated under the nominal defeat criteria.
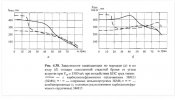
At 0 degrees, 3BM6 defeats 250mm RHA but as the target obliquity increases, the LOS depth of the perforation path of 3BM6 increases until around 63 degrees where it begins falling, finally ending at 82 degrees. This is a characteristic behaviour of long rod penetrators. Most importantly, it is shown in the graph that 3BM6 can defeat 160mm of RHA at 60 degrees, translating to a LOS thickness of 320mm.
Combat experience in the 1973 Yom Kippur conflict revealed that the M392A1 round (functionally identical to the basic M392) could not perform reliably on heavily sloped armour. This was quickly solved with a tungsten alloy tilting cap on the L28A1 and M392A2 in 1974 based on the technical solutions developed for the L52A1 round in the late 1960's. Both L28A1 and M392A1 were functionally identical and both could defeat 110mm of RHA steel at 60 degrees at 2,000 meters.
The L52 round could defeat 120mm of RHA at 60 degrees from a range of 1,830 meters, while the improved L52A2 round could defeat the same thickness of armour at a slightly increased range of 2,000 meters. At 1,000 meters, L52A2 could defeat 130mm of RHA at 60 degrees.
Despite lacking any heavy metal component whatsoever, 3BM6 was already enough to defeat the Chieftain at typical combat distances. According to a Soviet analysis of an Iranian Chieftain captured by the Iraqi army during the early part of the Iran-Iraq war, available here on
Andrei Tarasenko's website, btvt.info, the upper glacis and frontal turret armour of the Chieftain Mk. 5 could be defeated at a distance of 1,600 meters. The frontal cheeks of the turret could be pierced at 1,600 m, and the base of the turret could be pierced at 2,300 m. The upper front plate, an 85mm cast armour plate sloped at 70 degrees, could be defeated at 1,600 m, while the lower front plate could be defeated at more than 3 km. The table says 3 kilometers, since they did not bother to conduct testing past that distance but the velocity limit is listed as 1,000 m/s which corresponds to a distance of 5 km. Needless to say, these are excellent results, especially considering that it is achieved without the use of any tungsten at all in the construction of the projectile.
The performance of 3BM-6 on spaced armour is detailed in the table below. In the table below, the first column from the left shows the impact angle and the next three columns from the left list the spaced armour configurations: b1 and b2 denote the thickness of the first and second plates in millimeters, and L denotes the size of the air gap in millimeters. The fourth column from the right lists the velocity limit of 3BM6 for the spaced described armour configuration, and the third column from the right lists the velocity limit for a monolithic plate of the same thickness in steel (b1 + b2). The difference in the velocity limit is listed in the second column from the right. The first column on the right shows the difference in the velocity limits between the spaced armour configuration and a monolithic plate in percentage points, and also represents the improvement in mass efficiency.
As you can see, the maximum improvement in mass efficiency was attained using a 90-1000-100 configuration which was also the toughest target and showed an improvement of 9.1% compared to a monolithic plate of the same physical thickness (190mm). Needless to say, however, the 1.0-meter air gap of this configuration is completely impractical for tank armour, and the total thickness of the array considering its 45 degree angle is huge: 1,683mm thick. The improvement in mass efficiency from the other configurations are all less than around 6 percentage points, so from these results, it can be said that 3BM6 performs well for simple spaced armour with two steel layers within the range of angles of between 0 to 45 degrees. In practice, simple spaced armour such as the type implemented on the turrets of upgraded Leopard 1 tanks would be no challenge for 3BM6 at any plausible combat distance, nor would the spaced armour of the MBT-70 or KPz-70 (had they entered service).
This round made up the bulk of ammunition exported to client states, making it the most numerous type of APFSDS ammunition available to Egyptian and Syrian tank crews during the Yom Kippur war.